Within the metal construction industry, there are many reasons why marking is important. From code compliance to brand marketing and even packaging, adding the appropriate part or package marking to the production process can bring many benefits to a manufacturer: increased brand visibility, increased part adoption, inventory tracking and much more.
Purchasing the right marking system can be challenging. Fortunately, you can save yourself a trip to the office supply store because you won’t find it there. Unfortunately, setting up a marking system is far more complex than picking up a printer from the local office supply store. To start, there are several different types of marking technologies, each with its own specific applications, plus strengths and weaknesses.
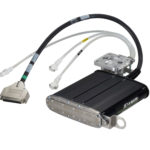
DOD printer image courtesy Matthews International
Drop-on-Demand (DOD) Printers
DOD printers have a print head composed of a number of electrically controlled valves to deliver ink to the material being marked. DOD printers generally have larger ink drops which leads to lower resolutions, but a print height range of 0.25 to 2 inches.
Recent advancement in DOD printers have brought new innovations such as the DOD valve technology for faster print marking over greater throw distances, and a larger print height range of 0.125 to 5 inches.
Continuous-Ink-Jet (CIJ) Printers
With a CIJ Printer, ink droplets are controlled by an electric charge to deliver smaller ink drop size and higher resolution print. CIJ printers do not ever touch the product, but spray the ink through the air one drop at a time in a pattern that, when a moving product passes, prints the code as programmed in the printer. Typical distance from the printer’s printhead to the product is 3/16 of an inch. Because CIJ printers are non-contact, they can print at high speeds, and also over curved or textured surfaces without degradation of print quality. CIJ Printers unfortunately have limited print heights of 0.125 – 0.5 inches.
Thermal Transfer Printers
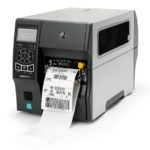
Thermal transfer printer image courtesy Zebra Technologies.
Most commonly used for marking high resolution images on flexible packaging film and labels, thermal transfer printers are highly customizable for a wide variety of materials and sizes. The thermal transfer printing process produces a very high resolution code onto the package that is easy to read and also ensures no degradation of the aesthetic quality of the packaging film artwork and design. Additional automation can be used to apply labels to parts or packages. Labels may not be the right option if there are wet or oily surfaces involved, or if there are heat treatments following the application of the label.
Permanent Marking Systems
There are times when a permanent marking solution is required, such as when there is a paint application or heat treatment after the part is marked, or perhaps a code compliance requirement.
There are several permanent marking systems, such as embossing, burning or laser printing. Check out our whitepaper on printing solutions for a more in-depth review.
Part and Package Marking Have Many Creative Benefits
With the use of BIM modeling software, printers can be considered an important element of the prefabrication process for the construction industry. Let’s say a house is being designed and all the metal studs are then ordered. When the stud order is placed, the studs for each wall will be packaged in its own bundle with all the correct quantities and lengths. Each part in the bundle can be properly marked with information that clearly indicates how to accurately complete the assembly of the studs. Similar to many of the “assemble-it-yourself” projects, marking can aid the prefab construction business by providing markers as clear guides.
Within the metal fabrication industry, part and package marking can also be used in many creative ways. Marking can be especially helpful in the event there are additional manufacturing steps required, for example welding. In this instance marks can provide the necessary instructions of where to weld and ensure the proper welds are performed.
How to Select the Right Print/Marking System
Now that we know the different types of print/marking systems, the next step is to answer some questions around what type of mark is needed, and the type of material being marked:
- What information needs to be marked?
- How often does the information change?
- What is the desired size of the marking?
- What is the quality level required?
- How durable/stable does the mark need to be?
- Will there be coolant or oils on the surface of the part before or after it is printed?
- Are there secondary processes that may affect the mark (ovens, painting, forming, etc.)?
- How fast is the machine running?
To help you with narrowing down which marking system to select, we’ve created a grid that outlines each marking system’s capabilities and suitability.
The grid is by no means exhaustive, and is meant to serve as a discussion guide during implementation. As you go about this process, be sure to remember that customer requests are varied, compliance standards get updated, and machine specifications change and can affect marking capabilities. Be sure to select a system that has the flexibility to grow with your needs.
About AMS Controls
AMS Controls provides a complete production management system and machine controls for manufacturers of panels, purlins, trim, studs and more. Since 1977, AMS Controls has sold 12,000+ controllers worldwide.
Industry leaders have chosen AMS Controls’ complete production management system to optimize the manufacturing of panels, purlins, trim, studs and structural products. Our controllers have been used with multiple leading folding machines including: Jorns, Schechtl, RAS, Roper Whitney, Bradbury and more. For more information on AMS Controls, visit www.amscontrols.com.