-
Technical Support
-
- A Case for Computer Integrated Manufacturing (CIM)
- Basic Methods of Length Control
- Benefits of Computer Integrated Manufacturing (CIM) - Deutsch
- Coil Handling
- Continuous Improvement - Tube & Pipe Journal
- Continuous Improvement in Roll Forming
- Encoder Tracking and Mounting
- Improving Roll Forming Operations
- Part Marking
- Roll Forming and Industry 4.0
- Roll Forming: The Four Basic Machine Types
- Servo Control for Improving Roll Formed Production
-
-
XL200 Series Support
-
- Battery Replacement
- Calibrating the Touchscreen of an XL200 Controller
- Extending XL200 Controls with PLC Integration
- Solving Memory Loss and Computer Lockup Problems
- Using Product Codes for Machine Positioning in the XL200 Series Controller
- Using Setup Configurations in the XL200 Series Controller
- Using Tool Configurations in the XL200 Series Controller
- XL200 Direct Ethernet Communication with Eclipse Classic
-
- Bar Code Scanners
- Bar Code Scanners for Data Entry
- Boosted Dies
- Calculating Press Reaction
- Checking Press Consistency with Oscilloscopes
- DIP Switch Configuration
- Punch Programming on the XL200
- Sending Saved Parameters or Tool Libraries from Eclipse Classic to XL Controller
- Understanding the XL200 Part Queue
- Using Product Codes for Machine Positioning in the XL200 Series Controller
- Using Setup Configurations in the XL200 Series Controller
- Using the Stitching Feature
- Using Tool Configurations in the XL200 Series Controller
- XL200 Error Codes
- XL200 Parameters
-
- BOSS Shear
- Brake & Hump - XL200CLU
- Calculating Press Reaction
- Checking Press Consistency with Oscilloscopes
- Closed Loop Flying Die / Die Accelerator
- Closed Loop Stopping
- Coil End Point
- Extending XL200 Controls with PLC Integration
- Open Loop Flying Die
- Open Loop Stopping / Feed-to-Stop
- Tailout Sensor
-
Eclipse Support
-
- A Case for Computer Integrated Manufacturing (CIM)
- Benefits of Computer Integrated Manufacturing (CIM) - Deutsch
- Coil Inventory Management with CIM
- Improving Production Capacity with Computer Integrated Manufacturing (CIM)
- Mistakes Happen! CIM for Mistake Prevention in Roll Forming
- Roll Forming and Industry 4.0
- The Quality Gap
-
- Automatically Starting Eclipse Classic
- Cable Specifications for RS Communication
- Coil Validation
- Creating an Eclipse Classic Package File
- Deleting Done Orders in Eclipse Classic
- Eclipse Classic Hardware Requirements
- Eclipse Classic Permissions - XLSecurity.exe
- Eclipse Connections
- Eclipse Data Exchange Options
- Establishing Communication with Eclipse
- Implementing Scrap, Delay, and Employee Codes in Eclipse Classic
- Interfacing Eclipse to External Data Systems - Importing and Exporting
- Material Code Query
- Missing Snapshot or Dates for Reports in Eclipse Classic
- Order Downloading Options in Eclipse Classic
- Performing Eclipse Classic Automatic Backups
- Performing Eclipse Classic Manual Backups
- Preventative Maintenance Made Easy
- Replacing a Controller / Recovery from a Memory Clear
- Reporting from Archived Data
- Reporting from Archived Data
- Requesting Eclipse Classic Support
- Sending Saved Parameters or Tool Libraries from Eclipse Classic to XL Controller
- Using a Proxy Server
- VLINX ESR901 Converter Installation and Configuration
- Show all articles ( 10 ) Collapse Articles
-
Pathfinder Support
-
- Calibrating the Backgauge - Pathfinder v2
- Calibrating the Machine - Pathfinder v2
- Calibrating the Touchscreen - Pathfinder v2
- Cleaning Controller Screens
- Extracting the Pathfinder SDF from a 5XXX/6XXX Machine
- Installing TeamViewer
- Pathfinder PC Backup/Restore/Import Procedure - Pathfinder v2
- Pathfinder PC BIOS Configuration - 5X00
- Pathfinder PC BIOS Configuration - 6X00
- Solving Memory Loss and Computer Lockup Problems
- XL250BB Backup/Restore Function
-
- FoldGuard Alignment Guide
- FoldGuard Alignment Guide - LZS-2-FG
- FoldGuard Brochure
- FoldGuard Encoder Installation Manual 1-02
- FoldGuard Frequently Asked Questions (FAQ)
- FoldGuard Operation Manual
- FoldGuard System Installation Manual 1-06
- FoldGuard System Installation Manual 1-07
- Laser Distortion Causes and Solutions Manual 1-02
-
MP Series Support
-
- MP300 Series Controller Manual
- MP300CL Series Controller Manual
- MP325 Manual
- MP328 Gripper Manual
- MP328CL Gripper Manual
- MP338 Backgauge Manual
- MP338DH Dual Backgauge Manual
- MP342 Manual
- MP343 Manual
- MP350PFD Manual
- MP450S Installation Guide
- MP465 Installation Guide
- MP465 Operator Manual
- MP465N Operator Manual NTM
-
-
Pathfinder Edge Support
-
- Accessing Pathfinder Edge
- Installing TeamViewer
- Logging into Pathfinder Edge
- Pathfinder Edge - Profile Object Format
- Pathfinder Edge Published API
- Print an Approval or Production Sheet - Edge
- Understanding Settings - Edge
- Using Categories and Subcategories - Edge
- Using the Profile Editor - Edge
- Using the Profile Library - Edge
-
Eclipse Pro Support
- Alert: Eclipse-COMM may be offline
- Alert: Material code XXXXXXXX does not correspond to a known material
- Checking the Status of Eclipse Pro Services
- Connect to Eclipse Pro from a Network Connected Device
- Eclipse Pro Hardware Requirements
- Eclipse Pro Product Sheet
- Eclipse Pro Product Sheet - Spanish
- Eclipse Pro Release Notes
- Eclipse Pro Scheduler
- Eclipse Pro Wallboard Andon App Setup
- Error: "Duplicate material codes. MATERIAL =..."
- Machine Performance Standards
- Nucor Case Study
- Requesting Eclipse Pro Support
- Schedule Sync Table Definition
- Updating Eclipse Pro
- Show all articles ( 1 ) Collapse Articles
-
Accessories Support
-
- 4805-XX and 3805-XX Encoder Cable Comparison
- BRKT-2 Assembly STEP File
- Encoder 10-Turn Test
- Encoder Bracket BRKT-1 Dimensional Drawing
- Encoder Bracket BRKT-2 Assembly Dimensional Drawing
- Encoder Bracket BRKT-2 Dimensional Drawing
- Encoder Brochure
- Encoder Sell Sheet
- Encoder Splitter 6390 Electrical Block Diagram
- Encoder Splitter 6390 Sell Sheet
- Encoder Splitter 6390 Shell STEP File
- Encoder Splitter Module 6390 Guide
- Encoder STEP File
- Encoder Tracking and Mounting
- Encoder Wheel KMW Dimensional Drawing
- Encoder Wheel PMW Dimensional Drawing
- KMW-12 Knurled Encoder Wheel STEP File
- NXXXX Encoder Assembly STEP File
- Scrap Reduction Using Two Encoders
- Troubleshooting Encoder Alignment
- Show all articles ( 5 ) Collapse Articles
-
- Indraworks DS Tuning Procedure (Analog) for CSB02_1 Control Sections
- Indraworks DS Tuning Procedure (Analog) for HCS01_1E Cs Servo Drives
- IndraWorks DS Tuning Procedure (EtherCAT) for CSB02_1 Control Sections
- IndraWorks DS Tuning Procedure (EtherCAT) for HCS01_1 Drives
- Indraworks DS Tuning Procedure (SERCOS II) for CSB01.1 Control Sections
-
Legacy Product Support
-
- About the MP401
- Cleaning Controller Screens
- CMP1000 Reference Manual
- CMP11-10 Reference Manual
- CMP12 Reference Manual
- MP100 Reference Manual
- MP101 Reference Manual
- MP101 v2 Reference Manual
- MP103 Reference Manual
- MP103 v3 Reference Manual
- MP237 Reference Manual
- MP257 Reference Manual
- MP37 Reference Manual
- MP38 Reference Manual
- MP39 Reference Manual
- MP401 User Manual
- MP43 Reference Manual
- MP44 Reference Manual
- MP450 Installation Guide
- MP450 Operator Manual
- MP450S Installation and Technical Reference Manual
- MP450S Installation Guide
- MP450S Operator Manual
- MP450Z Operator Manual
- MP46 Reference Manual
- MP465N Operator Manual NTM
- MP54 Reference Manual
- MP55 Reference Manual
- MP550 Operator Manual
- MP56 Reference Manual
- MP57 Reference Manual
- Show all articles ( 16 ) Collapse Articles
-
Calculating Press Reaction
Collect a notebook, pen, and calculator. During this procedure, the line speed displayed on the controller must be noted. Measurements must be taken in the order parts are produced from the machine. It might be helpful to have support personnel available to observe and record.
- Set Press Reaction Time to zero.
- Program two press operations (in the case of a shear, two part lengths). Be sure to program them at a distance that is long enough so that when the XL200 fires the press in automatic, the line is at speed. If the line is still accelerating up to speed, the test will be invalid. (If the machine supports in-line punching, program the shear and punch tool at the same offset distance for the purpose of the test. After the test, reprogram the punch tool to the correct physical distance).
- Perform a standing press operation (fire the press manually while the material is halted).
- Run the line.
- After the controller has fired the press twice, measure the distance from the standing press hit to the first automatic press hit. Then measure from the first automatic press hit to the second.
- Subtract the second length from the first.
- Divide the result by the line speed in feet per minute (meters per minute).
- Multiply the result by 5 (0.06 if using the metric system).
- The result is the Press Reaction Time.
If part lengths are inconsistent due to encoder tracking problems or press reaction variances, this test is a waste of time. Inconsistencies must be eliminated first before measurements to eliminate constant errors can be performed. To entertain any other methodology is an exercise in futility and frustration.
When performing the Press Reaction Calculation Procedure for the first time, it is often helpful to run at least 5 parts in a row. The first two can be used to calculate reaction time, if the last 4 parts are consistent.
Example:
Maintenance (Joe) is called to examine an open loop flying die machine. Larry, the machine operator, complains that the machine produces varying lengths on startup and sometimes during the production run. Upon examination, Joe can see that the XL200 was never programmed with a Shear Reaction value (or he suspects the value has been changed).
Joe begins by programming 5 parts at 60” (1524 mm). It is well known that this machine reaches speed after a short distance, so there is no need to program a longer part that might potentially become scrap. He sets the line to run at 150 fpm (46 mpm) for the purpose of the test.
Joe performs a Manual Shear operation to reference the cutoff, and then he runs the line. After 5 parts are produced, he halts the line and measures the parts in the order they were produced, first to last. His results are:
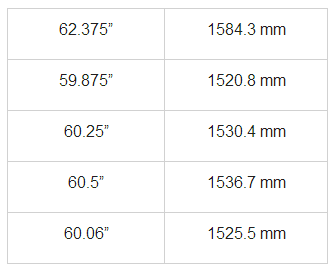
Based on the numbers, Joe can see that there is an overall length variance that he must address before he continues with any other efforts. He knows how critical the material encoder tracking is to the accuracy of the process, so he begins by checking the alignment of the encoder wheel and bracket to the material.
Joe finds the wheel to be significantly out of alignment and corrects the problem. He programs another 5 parts, performs a Manual Shear, and runs a second set of 60” (1524 mm) parts. This time, his results are:
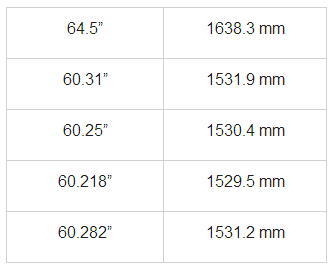
From the results, Joe is satisfied that the machine is performing consistently enough that he can now use the features built into the XL200 to eliminate the rest of the length issues. He runs through the procedure for calculating Press Reaction, using the average of the last 4 parts as his “second length”:
1st length – 2nd length = 4.235” (107.6 mm)
4.235” (107.6 mm) / 150 fpm (46 mpm) = 0.02823 (2.3528)
0.028233 (2.3528) · 5 (0.06) = 0.1412 s
Joe enters the value 0.1412 s into the Shear Reaction parameter in the XL200 controller. He also knows he can use the Calibrate Trim feature to remove the consistent 0.265” (6.73 mm) error from his overall length.
Now, when Joe turns the line over to Larry, production can expect part lengths to be consistent and accurate from first-to-last, even when Larry changes speeds during production.