-
Technical Support
-
- A Case for Computer Integrated Manufacturing (CIM)
- Basic Methods of Length Control
- Benefits of Computer Integrated Manufacturing (CIM) - Deutsch
- Coil Handling
- Continuous Improvement - Tube & Pipe Journal
- Continuous Improvement in Roll Forming
- Encoder Tracking and Mounting
- Improving Roll Forming Operations
- Part Marking
- Roll Forming and Industry 4.0
- Roll Forming: The Four Basic Machine Types
- Servo Control for Improving Roll Formed Production
-
-
XL200 Series Support
-
- Battery Replacement
- Calibrating the Touchscreen of an XL200 Controller
- Extending XL200 Controls with PLC Integration
- Solving Memory Loss and Computer Lockup Problems
- Using Product Codes for Machine Positioning in the XL200 Series Controller
- Using Setup Configurations in the XL200 Series Controller
- Using Tool Configurations in the XL200 Series Controller
- XL200 Direct Ethernet Communication with Eclipse Classic
-
- Bar Code Scanners
- Bar Code Scanners for Data Entry
- Boosted Dies
- Calculating Press Reaction
- Checking Press Consistency with Oscilloscopes
- DIP Switch Configuration
- Punch Programming on the XL200
- Sending Saved Parameters or Tool Libraries from Eclipse Classic to XL Controller
- Understanding the XL200 Part Queue
- Using Product Codes for Machine Positioning in the XL200 Series Controller
- Using Setup Configurations in the XL200 Series Controller
- Using the Stitching Feature
- Using Tool Configurations in the XL200 Series Controller
- XL200 Error Codes
- XL200 Parameters
-
- BOSS Shear
- Brake & Hump - XL200CLU
- Calculating Press Reaction
- Checking Press Consistency with Oscilloscopes
- Closed Loop Flying Die / Die Accelerator
- Closed Loop Stopping
- Coil End Point
- Extending XL200 Controls with PLC Integration
- Open Loop Flying Die
- Open Loop Stopping / Feed-to-Stop
- Tailout Sensor
-
Eclipse Support
-
- A Case for Computer Integrated Manufacturing (CIM)
- Benefits of Computer Integrated Manufacturing (CIM) - Deutsch
- Coil Inventory Management with CIM
- Improving Production Capacity with Computer Integrated Manufacturing (CIM)
- Mistakes Happen! CIM for Mistake Prevention in Roll Forming
- Roll Forming and Industry 4.0
- The Quality Gap
-
- Automatically Starting Eclipse Classic
- Cable Specifications for RS Communication
- Coil Validation
- Creating an Eclipse Classic Package File
- Deleting Done Orders in Eclipse Classic
- Eclipse Classic Hardware Requirements
- Eclipse Classic Permissions - XLSecurity.exe
- Eclipse Connections
- Eclipse Data Exchange Options
- Establishing Communication with Eclipse
- Implementing Scrap, Delay, and Employee Codes in Eclipse Classic
- Interfacing Eclipse to External Data Systems - Importing and Exporting
- Material Code Query
- Missing Snapshot or Dates for Reports in Eclipse Classic
- Order Downloading Options in Eclipse Classic
- Performing Eclipse Classic Automatic Backups
- Performing Eclipse Classic Manual Backups
- Preventative Maintenance Made Easy
- Replacing a Controller / Recovery from a Memory Clear
- Reporting from Archived Data
- Reporting from Archived Data
- Requesting Eclipse Classic Support
- Sending Saved Parameters or Tool Libraries from Eclipse Classic to XL Controller
- Using a Proxy Server
- VLINX ESR901 Converter Installation and Configuration
- Show all articles ( 10 ) Collapse Articles
-
Pathfinder Support
-
- Calibrating the Backgauge - Pathfinder v2
- Calibrating the Machine - Pathfinder v2
- Calibrating the Touchscreen - Pathfinder v2
- Cleaning Controller Screens
- Extracting the Pathfinder SDF from a 5XXX/6XXX Machine
- Installing TeamViewer
- Pathfinder PC Backup/Restore/Import Procedure - Pathfinder v2
- Pathfinder PC BIOS Configuration - 5X00
- Pathfinder PC BIOS Configuration - 6X00
- Solving Memory Loss and Computer Lockup Problems
- XL250BB Backup/Restore Function
-
- FoldGuard Alignment Guide
- FoldGuard Alignment Guide - LZS-2-FG
- FoldGuard Brochure
- FoldGuard Encoder Installation Manual 1-02
- FoldGuard Frequently Asked Questions (FAQ)
- FoldGuard Operation Manual
- FoldGuard System Installation Manual 1-06
- FoldGuard System Installation Manual 1-07
- Laser Distortion Causes and Solutions Manual 1-02
-
MP Series Support
-
- MP300 Series Controller Manual
- MP300CL Series Controller Manual
- MP325 Manual
- MP328 Gripper Manual
- MP328CL Gripper Manual
- MP338 Backgauge Manual
- MP338DH Dual Backgauge Manual
- MP342 Manual
- MP343 Manual
- MP350PFD Manual
- MP450S Installation Guide
- MP465 Installation Guide
- MP465 Operator Manual
- MP465N Operator Manual NTM
-
-
Pathfinder Edge Support
-
- Accessing Pathfinder Edge
- Installing TeamViewer
- Logging into Pathfinder Edge
- Pathfinder Edge - Profile Object Format
- Pathfinder Edge Published API
- Print an Approval or Production Sheet - Edge
- Understanding Settings - Edge
- Using Categories and Subcategories - Edge
- Using the Profile Editor - Edge
- Using the Profile Library - Edge
-
Eclipse Pro Support
- Alert: Eclipse-COMM may be offline
- Alert: Material code XXXXXXXX does not correspond to a known material
- Checking the Status of Eclipse Pro Services
- Connect to Eclipse Pro from a Network Connected Device
- Eclipse Pro Hardware Requirements
- Eclipse Pro Product Sheet
- Eclipse Pro Product Sheet - Spanish
- Eclipse Pro Release Notes
- Eclipse Pro Scheduler
- Eclipse Pro Wallboard Andon App Setup
- Error: "Duplicate material codes. MATERIAL =..."
- Machine Performance Standards
- Nucor Case Study
- Requesting Eclipse Pro Support
- Schedule Sync Table Definition
- Updating Eclipse Pro
- Show all articles ( 1 ) Collapse Articles
-
Accessories Support
-
- 4805-XX and 3805-XX Encoder Cable Comparison
- BRKT-2 Assembly STEP File
- Encoder 10-Turn Test
- Encoder Bracket BRKT-1 Dimensional Drawing
- Encoder Bracket BRKT-2 Assembly Dimensional Drawing
- Encoder Bracket BRKT-2 Dimensional Drawing
- Encoder Brochure
- Encoder Sell Sheet
- Encoder Splitter 6390 Electrical Block Diagram
- Encoder Splitter 6390 Sell Sheet
- Encoder Splitter 6390 Shell STEP File
- Encoder Splitter Module 6390 Guide
- Encoder STEP File
- Encoder Tracking and Mounting
- Encoder Wheel KMW Dimensional Drawing
- Encoder Wheel PMW Dimensional Drawing
- KMW-12 Knurled Encoder Wheel STEP File
- NXXXX Encoder Assembly STEP File
- Scrap Reduction Using Two Encoders
- Troubleshooting Encoder Alignment
- Show all articles ( 5 ) Collapse Articles
-
- Indraworks DS Tuning Procedure (Analog) for CSB02_1 Control Sections
- Indraworks DS Tuning Procedure (Analog) for HCS01_1E Cs Servo Drives
- IndraWorks DS Tuning Procedure (EtherCAT) for CSB02_1 Control Sections
- IndraWorks DS Tuning Procedure (EtherCAT) for HCS01_1 Drives
- Indraworks DS Tuning Procedure (SERCOS II) for CSB01.1 Control Sections
-
Legacy Product Support
-
- About the MP401
- Cleaning Controller Screens
- CMP1000 Reference Manual
- CMP11-10 Reference Manual
- CMP12 Reference Manual
- MP100 Reference Manual
- MP101 Reference Manual
- MP101 v2 Reference Manual
- MP103 Reference Manual
- MP103 v3 Reference Manual
- MP237 Reference Manual
- MP257 Reference Manual
- MP37 Reference Manual
- MP38 Reference Manual
- MP39 Reference Manual
- MP401 User Manual
- MP43 Reference Manual
- MP44 Reference Manual
- MP450 Installation Guide
- MP450 Operator Manual
- MP450S Installation and Technical Reference Manual
- MP450S Installation Guide
- MP450S Operator Manual
- MP450Z Operator Manual
- MP46 Reference Manual
- MP465N Operator Manual NTM
- MP54 Reference Manual
- MP55 Reference Manual
- MP550 Operator Manual
- MP56 Reference Manual
- MP57 Reference Manual
- Show all articles ( 16 ) Collapse Articles
-
Punch Programming on the XL200
“It can’t be that easy!”
We often hear these words after describing how to program punch patterns on the XL200 series controllers. This is especially true for customers who are used to spending hours calculating punch progressions by hand. This feature has been part of the XL series for nearly two decades and as a result, many of us at AMS Controls tend to take it for granted. We hope that this will give you an understanding of how our punching system works.
One of the great things about roll forming is the ability to add in-line punching to the operation. In most cases, manufacturers are able to eliminate all secondary operations so that the parts produced on the roll former are ready for use. We have seen many cases where the elimination of secondary operations led to tremendous improvements in throughput and profitability.
Benefits
The following are examples of the most common benefits of the XL200 series punching system:
- Simple programming directly from part drawings.
- Parametric approach allows one punch pattern to work for any part length.
- Seamlessly change part lengths and punch patterns on-the-fly, with no need to stop or create scrap between parts.
- On-the-fly target calculations allows for changes to schedule, automatic handling of coil changes, remaking of parts, etc.
- No cumulative errors.
Basic concept
With many controllers on the market, it is necessary for the customer to calculate the “punch progression”. The punch progression is the series of moves of the material and the activation of punches at the correct time to create the desired pattern. This can be time-consuming and math intensive since the relative distances between the punch tools must be accounted for in the calculations. With the XL series punch programming system, you simply tell the controller where on the part you want each tool to hit and the controller handles all of the calculations automatically and on-the-fly. Of course, it is also necessary to tell the controller the relative distances between the punch tools, but this is only done when configuring the controller for the first time.
Punch References
Punch locations can be referenced along the length of the part (X-axis) or across the width of the part (Y-axis) on machine that have movable punch tools. The following describes each of the ways punches can be referenced:
X-Axis
- Leading edge – The dimension from the leading edge (first edge to exit the machine) to the punch.
- Trailing edge – Distance from the trailing edge (last edge to exit the machine) to the punch.
- Center leading – Distance from the center of the part back towards the leading edge.
- Center trailing – Distance from the center of the part towards the trailing edge.
- Even spacing – This reference creates a series of holes that are evenly spaced. The series starts with a leading edge-referenced hole and continues to the trailing edge of the part or until the spacing limit is hit. Extra punches are added or removed depending on the part length.
- Spacing limit – This limits even spaced punches from getting within the specified distance of the trailing edge. It is used in cases where it is not desirable to have a hole too close to the end of the part.
Y-Axis
In a similar fashion, punches can be located anywhere across the width of the part relative to either edge or the centerline of the part: +Edge, +Center, -Center, -Edge.
Example
Here’s an example of how to program a simple part using all of the X-axis references. This diagram shows the layout of the punch tools and shear blade:
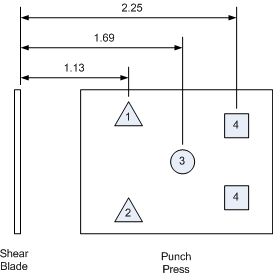
Here is the desired part:
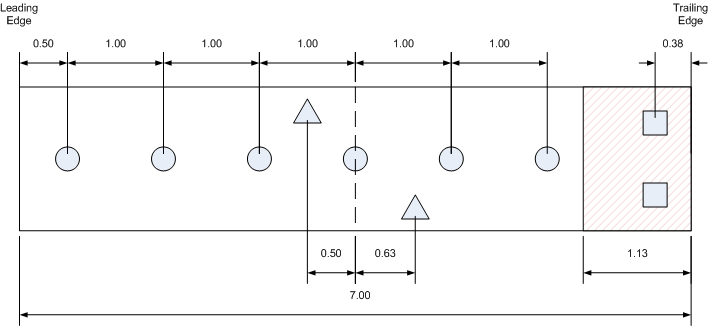
To program this part on the XL200, you would define the punch pattern as follows:
Pattern 1
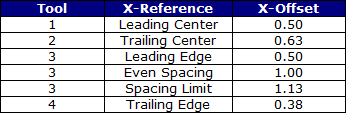
To make 50 of these parts, you would program a line item as follows:

For this to work, the punch tools must be correctly defined in the XL200 controller:

Some controllers only allow punches to be referenced relative to the leading edge of the part. While this can work fine for very simple cases, it means that a new punch pattern has to be created for every different part length. Since the XL200 can also reference punches from the trailing edge and the centerline, it is very easy to create a punch pattern that can be reused for all part lengths. The even spacing reference makes it a simple matter to handle parts with a series of holes.
Metal wall studs are a common example of this feature. These parts typically have holes spaced every 24 inches (or 600 mm) along their length. Even though they are sold in a wide range of lengths, with the XL200 you can define a simple pattern that works for all lengths:

Part Options
Many parts need to be produced in pairs with both a right and left hand part. A common example of this are track pieces for a residential garage door. Both sides receive the same punch pattern, but the pattern is reversed for one side as it is produced on the roll former. The XL200 part option feature makes it easy to program these types of parts. When a punch pattern is specified as part of a line item, you can select which orientation to use. The following are the available options:
- Right – This is the normal orientation (as programmed in the punch pattern).
- Left – This is the reversed orientation (the leading and trailing references are flipped).
- Alternating – With this option, the XL200 will produce both right and left handed parts alternating back and forth between parts (R, L, R, L, R, L…).
- Mirror – This rarely used option takes all punches between the leading edge and center and “mirrors” the punches to the other side of the part.
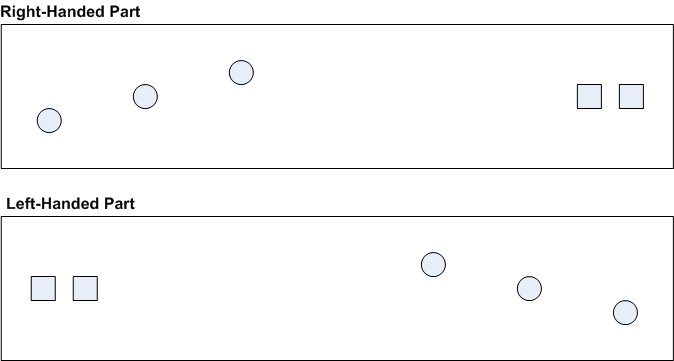
We hope this has helped you further understand the XL200 punch patterns function. If you have more questions, please contact Technical Support.