-
Technical Support
-
- A Case for Computer Integrated Manufacturing (CIM)
- Basic Methods of Length Control
- Benefits of Computer Integrated Manufacturing (CIM) - Deutsch
- Coil Handling
- Continuous Improvement - Tube & Pipe Journal
- Continuous Improvement in Roll Forming
- Encoder Tracking and Mounting
- Improving Roll Forming Operations
- Part Marking
- Roll Forming and Industry 4.0
- Roll Forming: The Four Basic Machine Types
- Servo Control for Improving Roll Formed Production
-
-
XL200 Series Support
-
- Battery Replacement
- Calibrating the Touchscreen of an XL200 Controller
- Extending XL200 Controls with PLC Integration
- Solving Memory Loss and Computer Lockup Problems
- Using Product Codes for Machine Positioning in the XL200 Series Controller
- Using Setup Configurations in the XL200 Series Controller
- Using Tool Configurations in the XL200 Series Controller
- XL200 Direct Ethernet Communication with Eclipse Classic
-
- Bar Code Scanners
- Bar Code Scanners for Data Entry
- Boosted Dies
- Calculating Press Reaction
- Checking Press Consistency with Oscilloscopes
- DIP Switch Configuration
- Punch Programming on the XL200
- Sending Saved Parameters or Tool Libraries from Eclipse Classic to XL Controller
- Understanding the XL200 Part Queue
- Using Product Codes for Machine Positioning in the XL200 Series Controller
- Using Setup Configurations in the XL200 Series Controller
- Using the Stitching Feature
- Using Tool Configurations in the XL200 Series Controller
- XL200 Error Codes
- XL200 Parameters
-
- BOSS Shear
- Brake & Hump - XL200CLU
- Calculating Press Reaction
- Checking Press Consistency with Oscilloscopes
- Closed Loop Flying Die / Die Accelerator
- Closed Loop Stopping
- Coil End Point
- Extending XL200 Controls with PLC Integration
- Open Loop Flying Die
- Open Loop Stopping / Feed-to-Stop
- Tailout Sensor
-
Eclipse Support
-
- A Case for Computer Integrated Manufacturing (CIM)
- Benefits of Computer Integrated Manufacturing (CIM) - Deutsch
- Coil Inventory Management with CIM
- Improving Production Capacity with Computer Integrated Manufacturing (CIM)
- Mistakes Happen! CIM for Mistake Prevention in Roll Forming
- Roll Forming and Industry 4.0
- The Quality Gap
-
- Automatically Starting Eclipse Classic
- Cable Specifications for RS Communication
- Coil Validation
- Creating an Eclipse Classic Package File
- Deleting Done Orders in Eclipse Classic
- Eclipse Classic Hardware Requirements
- Eclipse Classic Permissions - XLSecurity.exe
- Eclipse Connections
- Eclipse Data Exchange Options
- Establishing Communication with Eclipse
- Implementing Scrap, Delay, and Employee Codes in Eclipse Classic
- Interfacing Eclipse to External Data Systems - Importing and Exporting
- Material Code Query
- Missing Snapshot or Dates for Reports in Eclipse Classic
- Order Downloading Options in Eclipse Classic
- Performing Eclipse Classic Automatic Backups
- Performing Eclipse Classic Manual Backups
- Preventative Maintenance Made Easy
- Replacing a Controller / Recovery from a Memory Clear
- Reporting from Archived Data
- Reporting from Archived Data
- Requesting Eclipse Classic Support
- Sending Saved Parameters or Tool Libraries from Eclipse Classic to XL Controller
- Using a Proxy Server
- VLINX ESR901 Converter Installation and Configuration
- Show all articles ( 10 ) Collapse Articles
-
Pathfinder Support
-
- Calibrating the Backgauge - Pathfinder v2
- Calibrating the Machine - Pathfinder v2
- Calibrating the Touchscreen - Pathfinder v2
- Cleaning Controller Screens
- Extracting the Pathfinder SDF from a 5XXX/6XXX Machine
- Installing TeamViewer
- Pathfinder PC Backup/Restore/Import Procedure - Pathfinder v2
- Pathfinder PC BIOS Configuration - 5X00
- Pathfinder PC BIOS Configuration - 6X00
- Solving Memory Loss and Computer Lockup Problems
- XL250BB Backup/Restore Function
-
- FoldGuard Alignment Guide
- FoldGuard Alignment Guide - LZS-2-FG
- FoldGuard Brochure
- FoldGuard Encoder Installation Manual 1-02
- FoldGuard Frequently Asked Questions (FAQ)
- FoldGuard Operation Manual
- FoldGuard System Installation Manual 1-06
- FoldGuard System Installation Manual 1-07
- Laser Distortion Causes and Solutions Manual 1-02
-
MP Series Support
-
- MP300 Series Controller Manual
- MP300CL Series Controller Manual
- MP325 Manual
- MP328 Gripper Manual
- MP328CL Gripper Manual
- MP338 Backgauge Manual
- MP338DH Dual Backgauge Manual
- MP342 Manual
- MP343 Manual
- MP350PFD Manual
- MP450S Installation Guide
- MP465 Installation Guide
- MP465 Operator Manual
- MP465N Operator Manual NTM
-
-
Pathfinder Edge Support
-
- Accessing Pathfinder Edge
- Installing TeamViewer
- Logging into Pathfinder Edge
- Pathfinder Edge - Profile Object Format
- Pathfinder Edge Published API
- Print an Approval or Production Sheet - Edge
- Understanding Settings - Edge
- Using Categories and Subcategories - Edge
- Using the Profile Editor - Edge
- Using the Profile Library - Edge
-
Eclipse Pro Support
- Alert: Eclipse-COMM may be offline
- Alert: Material code XXXXXXXX does not correspond to a known material
- Checking the Status of Eclipse Pro Services
- Connect to Eclipse Pro from a Network Connected Device
- Eclipse Pro Hardware Requirements
- Eclipse Pro Product Sheet
- Eclipse Pro Product Sheet - Spanish
- Eclipse Pro Release Notes
- Eclipse Pro Scheduler
- Eclipse Pro Wallboard Andon App Setup
- Error: "Duplicate material codes. MATERIAL =..."
- Machine Performance Standards
- Nucor Case Study
- Requesting Eclipse Pro Support
- Schedule Sync Table Definition
- Updating Eclipse Pro
- Show all articles ( 1 ) Collapse Articles
-
Accessories Support
-
- 4805-XX and 3805-XX Encoder Cable Comparison
- BRKT-2 Assembly STEP File
- Encoder 10-Turn Test
- Encoder Bracket BRKT-1 Dimensional Drawing
- Encoder Bracket BRKT-2 Assembly Dimensional Drawing
- Encoder Bracket BRKT-2 Dimensional Drawing
- Encoder Brochure
- Encoder Sell Sheet
- Encoder Splitter 6390 Electrical Block Diagram
- Encoder Splitter 6390 Sell Sheet
- Encoder Splitter 6390 Shell STEP File
- Encoder Splitter Module 6390 Guide
- Encoder STEP File
- Encoder Tracking and Mounting
- Encoder Wheel KMW Dimensional Drawing
- Encoder Wheel PMW Dimensional Drawing
- KMW-12 Knurled Encoder Wheel STEP File
- NXXXX Encoder Assembly STEP File
- Scrap Reduction Using Two Encoders
- Troubleshooting Encoder Alignment
- Show all articles ( 5 ) Collapse Articles
-
- Indraworks DS Tuning Procedure (Analog) for CSB02_1 Control Sections
- Indraworks DS Tuning Procedure (Analog) for HCS01_1E Cs Servo Drives
- IndraWorks DS Tuning Procedure (EtherCAT) for CSB02_1 Control Sections
- IndraWorks DS Tuning Procedure (EtherCAT) for HCS01_1 Drives
- Indraworks DS Tuning Procedure (SERCOS II) for CSB01.1 Control Sections
-
Legacy Product Support
-
- About the MP401
- Cleaning Controller Screens
- CMP1000 Reference Manual
- CMP11-10 Reference Manual
- CMP12 Reference Manual
- MP100 Reference Manual
- MP101 Reference Manual
- MP101 v2 Reference Manual
- MP103 Reference Manual
- MP103 v3 Reference Manual
- MP237 Reference Manual
- MP257 Reference Manual
- MP37 Reference Manual
- MP38 Reference Manual
- MP39 Reference Manual
- MP401 User Manual
- MP43 Reference Manual
- MP44 Reference Manual
- MP450 Installation Guide
- MP450 Operator Manual
- MP450S Installation and Technical Reference Manual
- MP450S Installation Guide
- MP450S Operator Manual
- MP450Z Operator Manual
- MP46 Reference Manual
- MP465N Operator Manual NTM
- MP54 Reference Manual
- MP55 Reference Manual
- MP550 Operator Manual
- MP56 Reference Manual
- MP57 Reference Manual
- Show all articles ( 16 ) Collapse Articles
-
Calibrating the Machine – Pathfinder v2
Please note that this process applies to Pathfinders running version 2 software only. This does not apply to a Pathfinder running version 4 software. Contact Support for help with version 4 calibration.
Pathfinder’s Administrative Tools includes a Calibrate Machine function. When Pathfinder requires calibration, you will see “Waiting for Calibration Data” at the bottom of the screen.
To start the calibration process, click the Tools button and select Calibrate Machine. From this screen, you can calibrate the Bending Beam Position, Clamping Beam Position, Clamping Beam Pressure and Radius Adjustment.
See below for more information.
Referencing Absolute Encoders
Some machines have an absolute encoder on the Bending Beam, Clamping Beam and/or Radius Adjustment. Since the encoder is absolute, it does not need to be “reset” based on a switch. However, it does need to track all of the range of motion of the axis to which it is tied, with values between zero and its maximum.
If your machine has an absolute encoder on any of its axes, your calibration screen for each axis will have a Reference Encoder button. Pressing this button will reset the encoder to a value in the middle of its range of motion. If this button is not present, there is no encoder to reference.
Note: It is important that you reference the absolute encoder before continuing to calibrate each axis. Failure to do so could result in inaccurate calibration.
To reference an absolute encoder, move the axis to a position in the middle of its range of motion. Once there, click Reference Encoder on the calibration screen. This will reset the encoder to a value in the middle of its valid range. Then, when calibrating, you ensure that all of the feedback measurements that you are recording are above zero.
Please note that if you press Reference Encoder when the axis has already been calibrated, all calibration data for that axis is removed.
Clamping Beam Pressure (optional)
Clamping beam position must only be calibrated on machines with pressure transducer feedback devices. Calibrating the clamping beam pressure requires taking measurements across the total range of the clamping beam’s motion. To measure the clamping beam pressure, watch the pressure input reading in the top right of the screen.
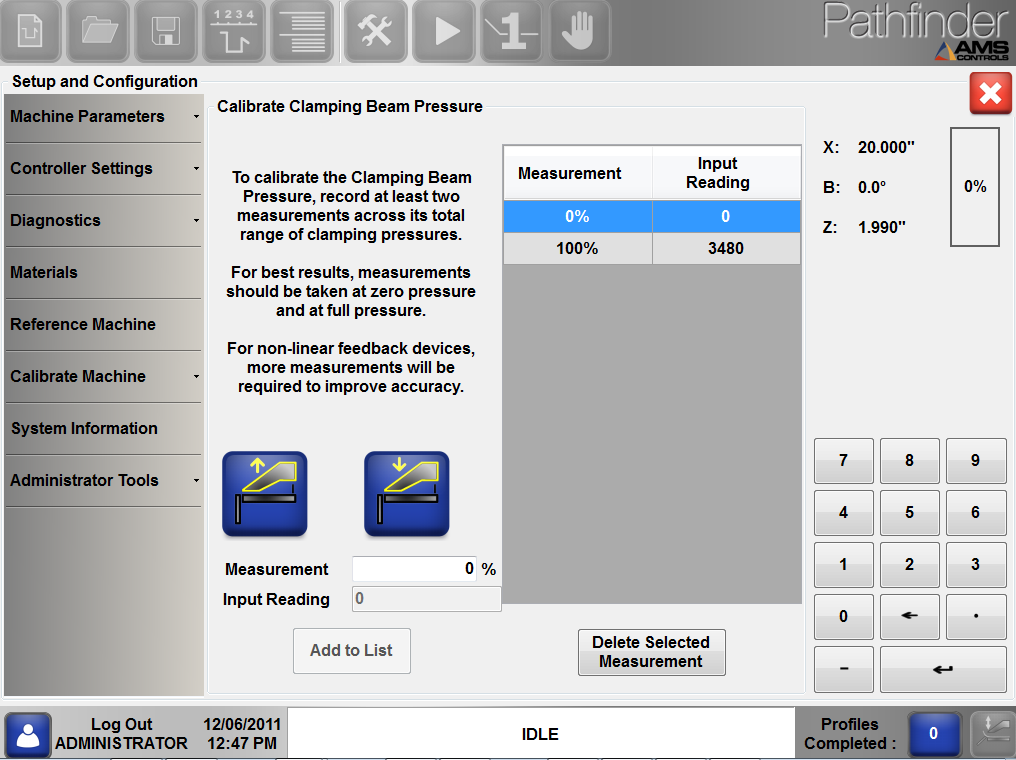
Clamping beam pressure calibration screen
Jog the clamping beam closed, until it is touching the table but not dramatically changing the input reading, then enter the pressure as 0% into the Measurement box, press Enter and select Add to List. Jog the clamping beam down as far as it will go, then enter the pressure as 100% into the Measurement box, press Enter and select Add to List.
Clamping Beam Position
Calibrating the clamping beam position requires taking measurements across the total range of the clamping beam’s motion. Use a caliper to measure the angle of the clamping beam.
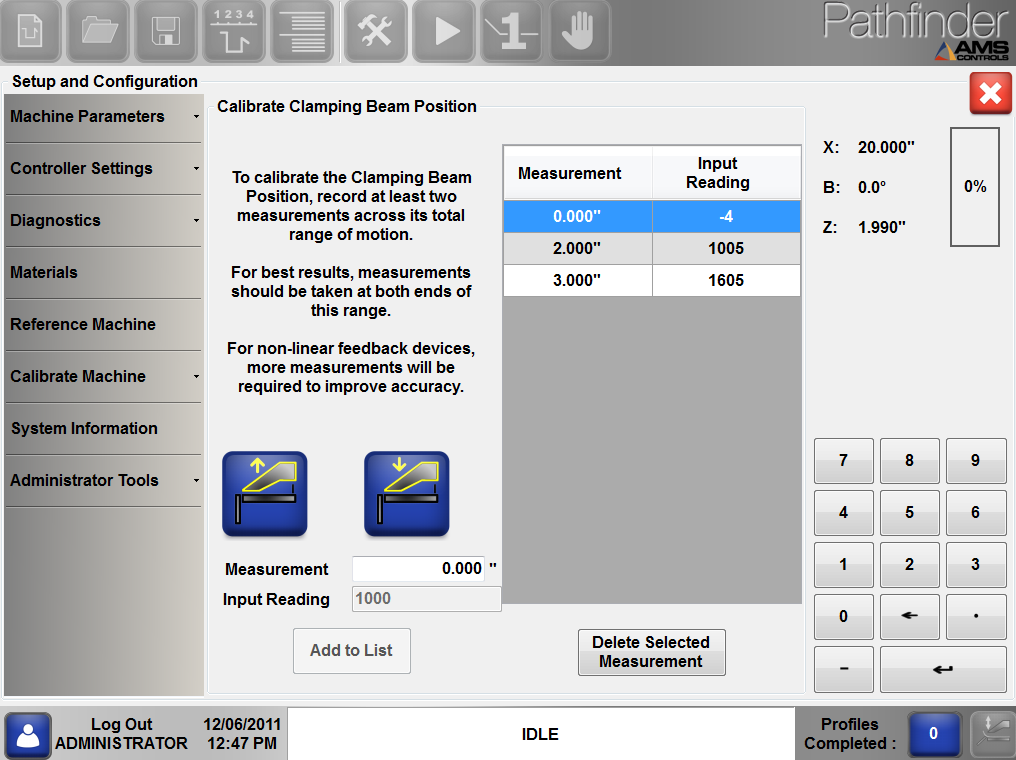
Clamping beam calibration screen
Jog the clamping beam to a position, then enter the measured position into the Measurement box, press Enter and select Add to List. Repeat this for several measurements all along the clamping beam’s range of motion. Feeler gauges may be helpful near the fully closed position. On machines with eccentric type clamping mechanisms, it is important to get many readings below the safety height for best results.
Remember, the more measurements you take, the more accurate the position.
Radius Adjustment Position (optional)
If you are using a folding machine that allows for Radius Adjustment, then this option will appear under Calibrate Machine.
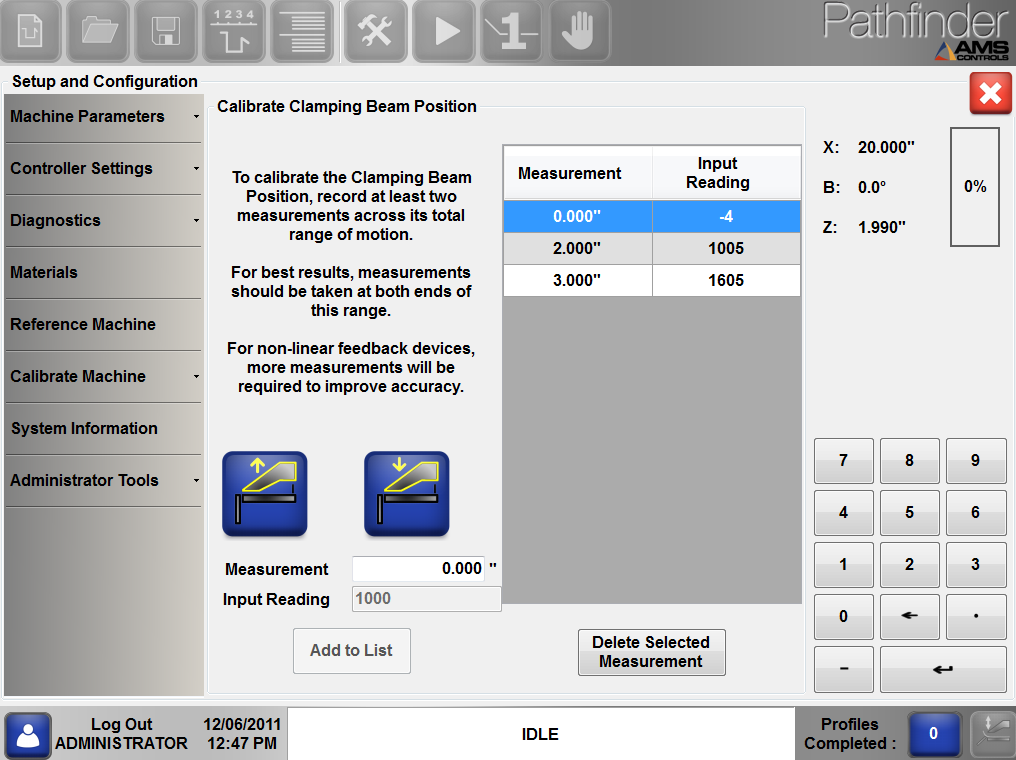
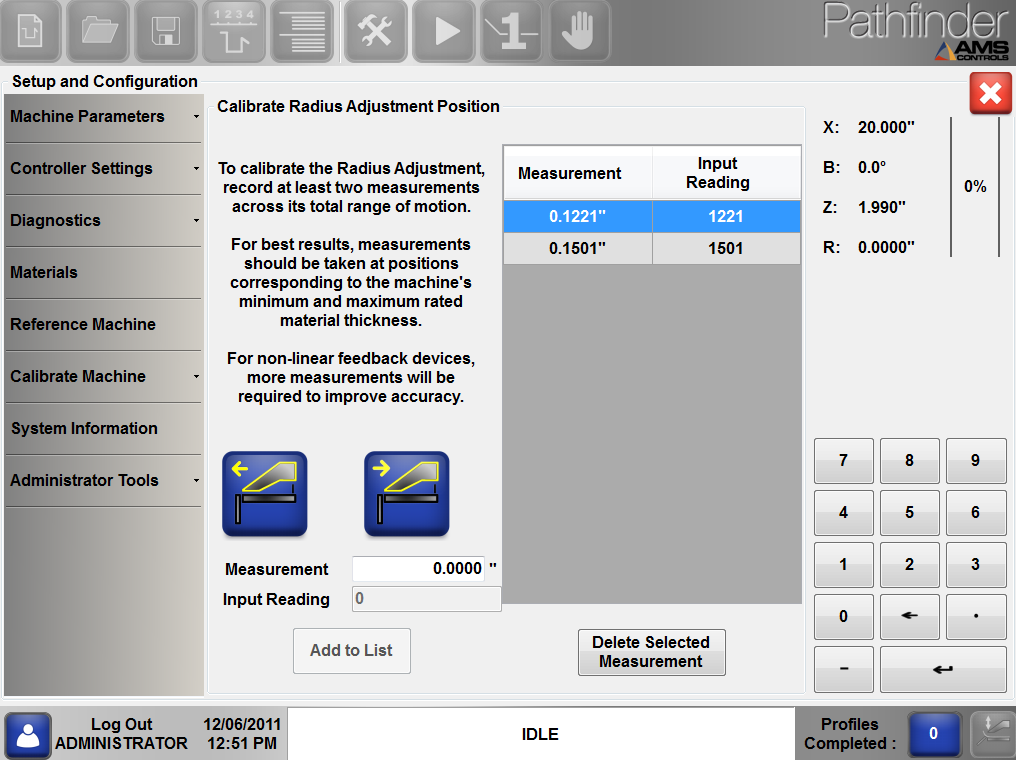
Calibrating Radius Adjustment
To calibrate the Radius Adjustment, the clamp must be open to a position greater than one inch. Jog the clamping beam as far away from the bending beam as possible and calibrate that to the maximum rating. Enter that measurement into the Measurement box, hit Enter and click Add to List to add the calibration data.
Then, jog the clamping beam as close to the bending beam as possible and calibrate that to the minimum rating. Enter that measurement into the Measurement box, hit Enter and click Add to List to add this data to the calibration table.
Bending Beam Position
Calibrating the bending beam position requires taking measurements across the total range of the bending beam’s motion. To measure the angle of the bending beam, use a magnetic inclinometer (available through woodworking stores).
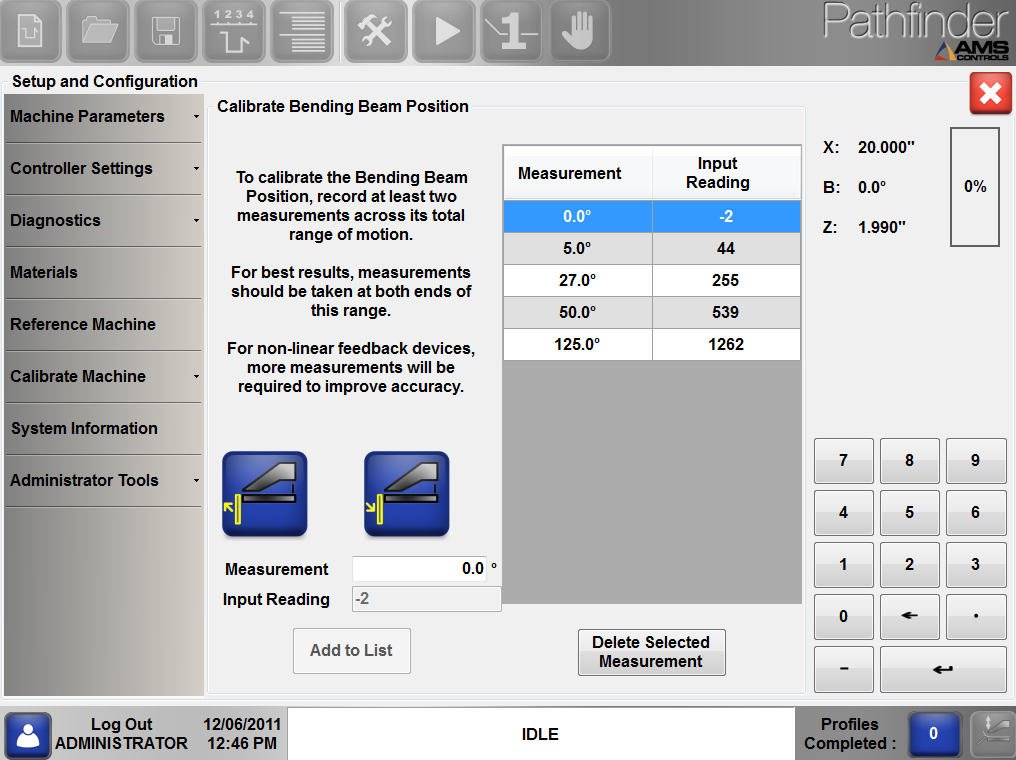
Bending Beam Calibration Screen
Jog the bending beam to a position and enter the measurement into the Measurement box and press Enter. Then select Add to List to add the measurement to the table. Repeat this for several angle positions, including both the highest and lowest range of motion for your particular machine.
Take the angle measurement for every 20 to 25 degrees for the most accurate calibration.
Note: Calibration measurements do not have to be taken in order. For example, you can take a measurement at 45°, then 100°, then jog back to 10° and take a measurement. The order of these measurements does not matter.
Remember, the more measurements you take, the more accurate the position.
Re-referencing the Clamping Beam
If the machine has a safety stop on the clamping beam, it is important to re-reference the clamping beam after calibration. This will ensure that the safety stop position is accurate. If your machine does not have a safety stop on the clamping beam, you can skip this step.
Return to the Reference Machine screen and select the Clamping Beam Down button until it is fully clamped. Follow any instructions that are shown on the screen. Once the Clamping Beam has been re-referenced, the machine will be ready to use.