-
Technical Support
-
- A Case for Computer Integrated Manufacturing (CIM)
- Basic Methods of Length Control
- Benefits of Computer Integrated Manufacturing (CIM) - Deutsch
- Coil Handling
- Continuous Improvement - Tube & Pipe Journal
- Continuous Improvement in Roll Forming
- Encoder Tracking and Mounting
- Improving Roll Forming Operations
- Part Marking
- Roll Forming and Industry 4.0
- Roll Forming: The Four Basic Machine Types
- Servo Control for Improving Roll Formed Production
-
-
XL200 Series Support
-
- Battery Replacement
- Calibrating the Touchscreen of an XL200 Controller
- Extending XL200 Controls with PLC Integration
- Solving Memory Loss and Computer Lockup Problems
- Using Product Codes for Machine Positioning in the XL200 Series Controller
- Using Setup Configurations in the XL200 Series Controller
- Using Tool Configurations in the XL200 Series Controller
- XL200 Direct Ethernet Communication with Eclipse Classic
-
- Bar Code Scanners
- Bar Code Scanners for Data Entry
- Boosted Dies
- Calculating Press Reaction
- Checking Press Consistency with Oscilloscopes
- DIP Switch Configuration
- Punch Programming on the XL200
- Sending Saved Parameters or Tool Libraries from Eclipse Classic to XL Controller
- Understanding the XL200 Part Queue
- Using Product Codes for Machine Positioning in the XL200 Series Controller
- Using Setup Configurations in the XL200 Series Controller
- Using the Stitching Feature
- Using Tool Configurations in the XL200 Series Controller
- XL200 Error Codes
- XL200 Parameters
-
- BOSS Shear
- Brake & Hump - XL200CLU
- Calculating Press Reaction
- Checking Press Consistency with Oscilloscopes
- Closed Loop Flying Die / Die Accelerator
- Closed Loop Stopping
- Coil End Point
- Extending XL200 Controls with PLC Integration
- Open Loop Flying Die
- Open Loop Stopping / Feed-to-Stop
- Tailout Sensor
-
Eclipse Support
-
- A Case for Computer Integrated Manufacturing (CIM)
- Benefits of Computer Integrated Manufacturing (CIM) - Deutsch
- Coil Inventory Management with CIM
- Improving Production Capacity with Computer Integrated Manufacturing (CIM)
- Mistakes Happen! CIM for Mistake Prevention in Roll Forming
- Roll Forming and Industry 4.0
- The Quality Gap
-
- Automatically Starting Eclipse Classic
- Cable Specifications for RS Communication
- Coil Validation
- Creating an Eclipse Classic Package File
- Deleting Done Orders in Eclipse Classic
- Eclipse Classic Hardware Requirements
- Eclipse Classic Permissions - XLSecurity.exe
- Eclipse Connections
- Eclipse Data Exchange Options
- Establishing Communication with Eclipse
- Implementing Scrap, Delay, and Employee Codes in Eclipse Classic
- Interfacing Eclipse to External Data Systems - Importing and Exporting
- Material Code Query
- Missing Snapshot or Dates for Reports in Eclipse Classic
- Order Downloading Options in Eclipse Classic
- Performing Eclipse Classic Automatic Backups
- Performing Eclipse Classic Manual Backups
- Preventative Maintenance Made Easy
- Replacing a Controller / Recovery from a Memory Clear
- Reporting from Archived Data
- Reporting from Archived Data
- Requesting Eclipse Classic Support
- Sending Saved Parameters or Tool Libraries from Eclipse Classic to XL Controller
- Using a Proxy Server
- VLINX ESR901 Converter Installation and Configuration
- Show all articles ( 10 ) Collapse Articles
-
Pathfinder Support
-
- Calibrating the Backgauge - Pathfinder v2
- Calibrating the Machine - Pathfinder v2
- Calibrating the Touchscreen - Pathfinder v2
- Cleaning Controller Screens
- Extracting the Pathfinder SDF from a 5XXX/6XXX Machine
- Installing TeamViewer
- Pathfinder PC Backup/Restore/Import Procedure - Pathfinder v2
- Pathfinder PC BIOS Configuration - 5X00
- Pathfinder PC BIOS Configuration - 6X00
- Solving Memory Loss and Computer Lockup Problems
- XL250BB Backup/Restore Function
-
- FoldGuard Alignment Guide
- FoldGuard Alignment Guide - LZS-2-FG
- FoldGuard Brochure
- FoldGuard Encoder Installation Manual 1-02
- FoldGuard Frequently Asked Questions (FAQ)
- FoldGuard Operation Manual
- FoldGuard System Installation Manual 1-06
- FoldGuard System Installation Manual 1-07
- Laser Distortion Causes and Solutions Manual 1-02
-
MP Series Support
-
- MP300 Series Controller Manual
- MP300CL Series Controller Manual
- MP325 Manual
- MP328 Gripper Manual
- MP328CL Gripper Manual
- MP338 Backgauge Manual
- MP338DH Dual Backgauge Manual
- MP342 Manual
- MP343 Manual
- MP350PFD Manual
- MP450S Installation Guide
- MP465 Installation Guide
- MP465 Operator Manual
- MP465N Operator Manual NTM
-
-
Pathfinder Edge Support
-
- Accessing Pathfinder Edge
- Installing TeamViewer
- Logging into Pathfinder Edge
- Pathfinder Edge - Profile Object Format
- Pathfinder Edge Published API
- Print an Approval or Production Sheet - Edge
- Understanding Settings - Edge
- Using Categories and Subcategories - Edge
- Using the Profile Editor - Edge
- Using the Profile Library - Edge
-
Eclipse Pro Support
- Alert: Eclipse-COMM may be offline
- Alert: Material code XXXXXXXX does not correspond to a known material
- Checking the Status of Eclipse Pro Services
- Connect to Eclipse Pro from a Network Connected Device
- Eclipse Pro Hardware Requirements
- Eclipse Pro Product Sheet
- Eclipse Pro Product Sheet - Spanish
- Eclipse Pro Release Notes
- Eclipse Pro Scheduler
- Eclipse Pro Wallboard Andon App Setup
- Error: "Duplicate material codes. MATERIAL =..."
- Machine Performance Standards
- Nucor Case Study
- Requesting Eclipse Pro Support
- Schedule Sync Table Definition
- Updating Eclipse Pro
- Show all articles ( 1 ) Collapse Articles
-
Accessories Support
-
- 4805-XX and 3805-XX Encoder Cable Comparison
- BRKT-2 Assembly STEP File
- Encoder 10-Turn Test
- Encoder Bracket BRKT-1 Dimensional Drawing
- Encoder Bracket BRKT-2 Assembly Dimensional Drawing
- Encoder Bracket BRKT-2 Dimensional Drawing
- Encoder Brochure
- Encoder Sell Sheet
- Encoder Splitter 6390 Electrical Block Diagram
- Encoder Splitter 6390 Sell Sheet
- Encoder Splitter 6390 Shell STEP File
- Encoder Splitter Module 6390 Guide
- Encoder STEP File
- Encoder Tracking and Mounting
- Encoder Wheel KMW Dimensional Drawing
- Encoder Wheel PMW Dimensional Drawing
- KMW-12 Knurled Encoder Wheel STEP File
- NXXXX Encoder Assembly STEP File
- Scrap Reduction Using Two Encoders
- Troubleshooting Encoder Alignment
- Show all articles ( 5 ) Collapse Articles
-
- Indraworks DS Tuning Procedure (Analog) for CSB02_1 Control Sections
- Indraworks DS Tuning Procedure (Analog) for HCS01_1E Cs Servo Drives
- IndraWorks DS Tuning Procedure (EtherCAT) for CSB02_1 Control Sections
- IndraWorks DS Tuning Procedure (EtherCAT) for HCS01_1 Drives
- Indraworks DS Tuning Procedure (SERCOS II) for CSB01.1 Control Sections
-
Legacy Product Support
-
- About the MP401
- Cleaning Controller Screens
- CMP1000 Reference Manual
- CMP11-10 Reference Manual
- CMP12 Reference Manual
- MP100 Reference Manual
- MP101 Reference Manual
- MP101 v2 Reference Manual
- MP103 Reference Manual
- MP103 v3 Reference Manual
- MP237 Reference Manual
- MP257 Reference Manual
- MP37 Reference Manual
- MP38 Reference Manual
- MP39 Reference Manual
- MP401 User Manual
- MP43 Reference Manual
- MP44 Reference Manual
- MP450 Installation Guide
- MP450 Operator Manual
- MP450S Installation and Technical Reference Manual
- MP450S Installation Guide
- MP450S Operator Manual
- MP450Z Operator Manual
- MP46 Reference Manual
- MP465N Operator Manual NTM
- MP54 Reference Manual
- MP55 Reference Manual
- MP550 Operator Manual
- MP56 Reference Manual
- MP57 Reference Manual
- Show all articles ( 16 ) Collapse Articles
-
Troubleshooting Encoder Alignment
Encoder and material tracking problems account for most product length variations on computer controlled roll forming lines. From the perspective of a length control system, all information regarding the material – direction, speed, distance traveled – comes from a single point, where the encoder measuring wheel contacts the material. Proper tracking of the encoder measuring wheel is therefore critical to machine performance.
Variance can come from sources other than the measuring system. However, these sources are less likely, and tend to be specific to the machine application type. The encoder system should always be examined first when troubleshooting length variance.
This troubleshooting article has been developed specifically for the AMS Controls Encoder. Troubleshooting non-AMS Controls encoders is not covered in this article.
Note: The procedures described in this handbook must be performed only by trained, certified industrial electricians. While AMS Controls has taken all reasonable care to develop safe procedures, it accepts no responsibility for injuries, damages, death or destruction to persons or equipment caused as a result of not closely following these instructions.
Removing Power from the System
When required to remove power from the system you must, turn the disconnect on the Auxiliary Electrical Box to the OFF position. This removes power from all the aux box components except the disconnect itself.
DANGER! Turning the power off at the main operator’s station does not remove all power from the system.
Check the Encoder Wheel for Perpendicular Alignment
Use a machinist’s square to check an encoder wheel for perpendicular alignment. The encoder wheel needs to be square (perpendicular) to the material surface on which it rides to ensure proper tracking.
Equipment Required
- Machinist’s square
Note: Carpenter’s squares are not square enough to be used to test for perpendicular positioning. It is important to have a proper machinist’s square for this test to be accurate.
Check for Perpendicular Alignment
- Place the base of the machinist’s square on the material surface that the encoder contacts.
- Slide the square toward the side of the encoder wheel until it just makes contact with the encoder wheel.
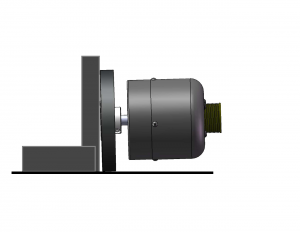
Figure 1: Machinist’s Square Showing a Gap, Indicating the Encoder Wheel is not Perpendicular
Examine the wheel and square from the front (looking head-on at the rim).
- If there is no gap between the encoder wheel and the machinist’s square, the encoder wheel is perpendicular to he material surface.
- If any gap is visible between the encoder wheel and the machinist’s square’s edge, the encoder wheel is not perpendicular to the material surface.
Check the Encoder Wheel for Parallel Alignment
Use a straight-edge and calipers to check an encoder wheel for parallel alignment.
Equipment Required
- Straight-edge or metal ruler
- Calipers
Check for Parallel Alignment
Lay the straight-edge along the wheel in the direction of material flow and draw a line along the length of the straight-edge.
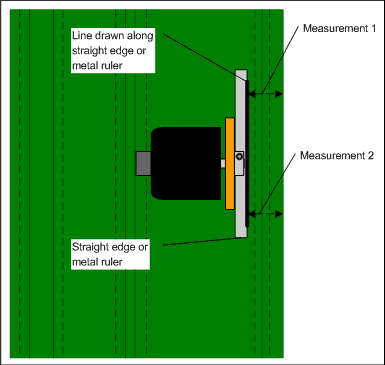
Figure 2: Testing for Parallel Alignment
2. If the measuring wheel is out of alignment, the error will be exaggerated by this line.
3. Using a set of calipers, the distance from each end of the line to the edge of the material should be measured.
The difference between the two measures should be less than 0.010” (0.254 mm) over 12” (304.8 mm).
If the error is greater than 0.010” (0.254 mm), the encoder bracket assembly should be realigned.
Note: Alignment should be rechecked each time the encoder bracket is loosened and retightened.
Oscilloscope Test
Use a two-channel Oscilloscope (O-scope) to verify the appearance of the signals coming from the encoder. Use the O-scope any time that:
- There are no counts coming from the encoder.
- You suspect the counts from the encoder are incorrect.
- Noise may be interfering with the counts.
Equipment Required
- Probe cables
- Oscilloscope (two channel with invert and add functions)
Note: To properly view the encoder signals, you must use a two-channel O-scope with both invert and add functions. Without these functions, your results will not match what is shown below.
Perform the O-Scope Test
- Connect the O-scope’s ground reference to the encoder’s ground circuit.
Note: To perform this test, you must use an encoder (or digital) ground. Grounding this way avoids “floating” at the same voltage, so the signal will be visible.
- Connect one probe to the A-channel.
- Connect the second ground reference of the scope to the encoder’s ground circuit.
- Connect the second probe to the B-channel. The PC screen displays a wave form for the encoder signal:
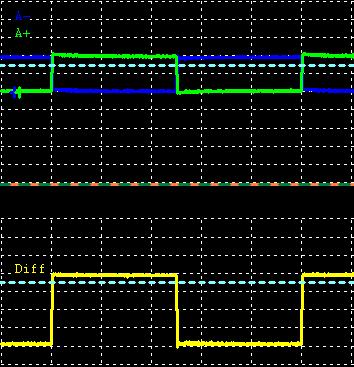
Figure 3 : Encoder Wave Form Displayed on the Oscilloscope (O-scope)
The display is typical of quadrature, showing the A-channel and B-channel 90° out of phase with each other, with the B-channel transitioning halfway through the A-channel’s wave.
– A leading B (A to the left of B) indicates the encoder is moving in the positive (forward) direction.
– B leading A (B to the left of A) indicates the encoder is moving in the negative (reverse) direction.
The smooth squared-off forms of the wave indicate clean pulses; spiking, wobbly or jagged waves indicate noise interfering with the signal. If you have spiking, wobbly or jagged waves, contact AMS Technical Support for further guidance.
Verify Encoder Counts (10-Turn Test)
Perform a 10-turn test to verify that an encoder is counting accurately. This test checks the internal hardware of the encoder, the cable from the encoder to the control system and the encoder circuits on the machine controller.
If all hardware is “good” as tested, but length variance persists, check the encoder tracking.